Intelligente Getriebe, intelligent verkabelt mit EPLAN
Mit stufenlosen Automatikgetrieben hilft die VDS Getriebe GmbH Herstellern landwirtschaftlicher und kommunaler Nutzfahrzeuge, deren Effizienz und Lebensdauer zu heben. Unter Verwendung patentierter, modularer Elemente modellspezifisch entwickelt, sind die Getriebe mechatronische Einheiten mit einem Antriebsmanagement, das vom Motor bis zur Radnabe reicht. Die Entwicklung der elektrotechnischen Komponente erfolgt seit Sommer 2014 mit EPLAN Electric P8 für die Schaltplanerstellung und mit EPLAN Harness proD für die Kabelbäume. Das integrierte 3D-Werkzeug gestattet die Parallelisierung der mechanischen und elektrischen Entwicklung und führt zu einer wesentlichen Verkürzung der Time-to-Market.
Wer schon einmal mit einem stufenlos angetriebenen Auto gefahren ist, kennt das Gefühl, vom Stand bis zur Höchstgeschwindigkeit unterbrechungsfrei beschleunigen zu können, ohne ein einziges Mal zu schalten. Die Motorleistung bei allen Geschwindigkeiten gleichmäßig vom Verbrennungsmotor auf die Räder zu übertragen, bringt optimales Fahrverhalten. Das macht Getriebe erforderlich, deren Übersetzungsverhältnis sich kontinuierlich anpassen lässt.
Nie wieder schalten
Seit Kraftfahrzeuge gebaut werden, gibt es Bestrebungen, Getriebe stufenlos auszuführen. Dabei geht es um mehr als nur den Komfortgewinn für die Fahrer. Speziell in Bereichen wie der Landwirtschaft, in denen Fahrzeuge in Extremsituationen an der Reibungsgrenze operieren, kann die Unterbrechung der Kraftübertragung durch Schaltvorgänge zu Rädergleiten führen. Die Folge wäre ein Abrutschen oder Hängenbleiben. „Die Zeit ist reif für effiziente Antriebssysteme. Nicht nur in PKWs und LKWs, in welchen bei der Suche nach Einsparungen im Treibstoffverbrauch immer aufwändigere Systeme generiert werden, sondern auch in Bau- und Arbeitsmaschinen“, sagt Dipl.-Ing. Heinz Aitzetmüller. Er hat sich der Entwicklung von stufenlosen Automatikgetrieben (Continuously Variable Transmission; CVT) verschrieben und 2009 in Wolfern bei Steyr (OÖ) die VDS Getriebe GmbH gegründet. „In Traktoren sind Stufenlosgetriebe mit hydrostatisch-mechanischer Leistungsverzweigung seit Jahren auf dem Markt und beweisen täglich, dass Effizienz und Stufenlosigkeit kein Widerspruch sein müssen.“ Aitzetmüller weiß, wovon er spricht, schließlich war er vor der Gründung von VDS (Variable Drive Systems) bei seinem früheren Dienstgeber maßgeblich an der Entwicklung solcher Getriebe beteiligt. „Auf diesem Gebiet gibt es kein Standardprodukt, VDS entwickelt das passende Getriebe für den jeweiligen Anwendungsfall“, sagt er. „Nur so ist der Spagat zwischen optimaler Leistungsausnutzung, maximaler Treibstoffeffizienz und vertretbaren Herstellkosten zu schaffen.“
Mechatronische Einheiten
Der Schlüssel dazu liegt laut Aitzetmüller in einem ausgewogenen Verhältnis der Leistungsanteile, die in dem leistungsverzweigten Getriebe mechanisch bzw. über den hydrostatischen oder elektrischen Variator übertragen werden. Erst die optimale Kombination der Leistungsstränge vom Motor bis zur Radnabe bringt Endkunden den vollen Nutzen der Technologie. Die Zusammenführung der Leistungsströme sowie die Steuerung des Übersetzungsverhältnisses erfolgen mittels mehrerer Planetengetriebe. Die Schaltvorgänge, aber auch die Ansteuerung der Variatoren, erfolgen über ein elektronisches Antriebsstrang-Managementsystem. Proportionalventile zur Ansteuerung des Hydrostaten und der Lamellenkupplungen sowie knapp 20 direkt an den rotierenden Komponenten verbaute Sensoren zur Erfassung etwa von Drehzahlen und Drücken machen die patentierten VTP- und VPD-Getriebe zu komplexen mechatronischen Einheiten.
Gesucht: Mechatronisches Werkzeug
„Solange es ‚nur‘ um die Verkabelung der Getriebe selbst ging – das Steuergerät wird als gekapselte Einheit extern angebracht – und die Serienüberleitung kundenseitig erfolgte, konstruierten wir die Kabelbäume rein mechanisch“, sagt DI (FH) Jürgen Fehringer, Leiter Software bei VDS. „Als uns ein Kunde bat, neben dem Getriebe auch die Steuerung und damit auch die Verkabelung für den gesamten Antriebsstrang seines Allrad-Kommunalfahrzeuges bis zur Serienreife zu entwickeln, war uns klar, dass wir bei unseren Konstruktionswerkzeugen aufrüsten mussten.“ „Unser Ziel war, ein mechatronisches Werkzeug zu finden, mit dem die Entwicklung der Kabelbäume ausgehend vom Schaltplan einerseits und der mechanischen Konstruktion andererseits in 3D erfolgt“, berichtet Konstrukteur Davidson Pilsner. „Wir waren von Beginn an überzeugt, dass sich nur durch Arbeiten am 3D-Modell teure Prototypen und/oder Fehlversuche vermeiden lassen, sodass die Entwicklung ohne Qualitätseinbußen in der gewünschten kurzen Zeit zu schaffen ist.“ „Die Auswahl an passenden Software-Tools war überraschend groß“, erinnert sich Davidson Pilsner. Unter anderem ist für das im Haus verwendete maschinenbauliche 3D-CAD System ein entsprechendes Add-on Produkt zu haben. „Das scheint sich jedoch, seiner Komplexität und seinem Preis nach zu urteilen, eher für den Aufbau der Verkabelung ganzer Flugzeuge in weltweit zusammenarbeitenden Teams zu eignen“, schmunzelt Jürgen Fehringer. „Bei meinen Internet-Recherchen im Frühjahr 2014 bin ich auf EPLAN Harness proD gestoßen, ein Produkt, das besser zu unserer Firmengröße mit 22 Mitarbeitern passt.“
Elektrokonstruktion ab dem Schaltplan
Mit EPLAN Harness proD hatten die Techniker von VDS ein höchst komfortables Werkzeug für die effiziente Kabelbaumentwicklung in 3D gefunden, das die Daten der Mechanik- und Elektrokonstruktion in einem System verbindet. Ein wesentliches Entscheidungskriterium war die Möglichkeit, durch Kombination mit EPLAN Electric P8 den elektrotechnischen Teil der Produktentwicklung mit der Erstellung des Schaltplans zu beginnen und im weiteren Verlauf der Konstruktion durchgängig auf einheitliche Elektrotechnik-Daten zuzugreifen. Präsentationen mit direktem Bezug zu den besonderen Aufgabenstellungen von VDS überzeugten, und so fiel die Entscheidung zugunsten einer Installation von EPLAN Electric P8 und EPLAN Harness proD im Sommer 2014. „Nach erfolgter Grundschulung habe ich mit dem dabei erlangten Wissen noch einmal Vergleiche mit alternativen Produkten angestellt“, berichtet Davidson Pilsner. „Der Vergleich hat die Richtigkeit der Entscheidung bestätigt, EPLAN Harness proD erlaubt an praktisch allen Stellen ein wesentlich flüssigeres Arbeiten.“
Konsistente Daten ohne Doppelerfassung
Der Arbeitsablauf ist klar strukturiert: Zunächst werden – meist von Jürgen Fehringer – in EPLAN Electric P8 der Schaltplan und daraus abgeleitete Materiallisten erstellt. Dessen Daten übernimmt Davidson Pilsner, der hauptsächlich mit EPLAN Harness proD arbeitet, per XML-Schnittstelle in die Kabelbaum-Software, wo sie mit den Informationen des mechanischen Systems gekoppelt werden. „Da dieser Importvorgang beliebig wiederholt werden kann, entfällt – vor allem bei nachträglichen Änderungen an der Elektrik – viel manuelle Datenpflege“, freut er sich. „Somit ist gewährleistet, dass alle auf demselben Stand der Daten sind; Inkonsistenzen und die dadurch verursachten Fehler können praktisch ausgeschlossen werden.“ Auch die Möglichkeit, Daten von Steckern und anderen Bauteilen aus Herstellerkatalogen zu importieren, erspart eine Menge Arbeit und schaltet Fehlerquellen aus. Gleiches gilt für die Ausgabe von Längen, Querschnitten und Kennzeichnungsinformationen für die einzelnen Kabel und Drähte, die wahlweise als PDF für die Werkstatt oder als Datensätze für EPLAN Electric P8 oder für Konfektioniermaschinen erfolgen kann.
Parallele mechatronische Entwicklung
Nach dem ersten, ohne Schwierigkeiten innerhalb der Zeitvorgaben fertiggestellten Projekt lässt sich über die direkte Zeitersparnis bei der Konstruktion des Kabelbaums und der Nagelbretter noch keine repräsentative Aussage treffen. Immerhin mussten sich beide Techniker parallel zur eigentlichen Arbeit erst in die neuen Softwarewerkzeuge einarbeiten und Routine aufbauen. Auch die erheblichen Effekte der Wiederverwendung bereits konstruierter Teile bleiben bei einem Erstprojekt völlig aus. „Der eigentliche Nutzeffekt ist die Möglichkeit, den Entwicklungsprozess unserer komplexen mechatronischen Produkte völlig umzustellen“, sagt Jürgen Fehringer. „Früher konnte der Kabelbaum erst hergestellt werden, nachdem der mechanische Prototyp fertiggestellt war.“ Dazu wurden erst am Prototyp Messungen durchgeführt und auf dieser Basis die Leitungsverlegung festgelegt. Oft genug waren mechanische Änderungen die Folge, weil z.B. kein Platz für eine Kabeldurchführung war. Heute erfolgt die Kabelbaumentwicklung parallel zur mechanischen Konstruktion und in Abstimmung mit dieser. Auf diese Weise lassen sich viele Überprüfungen ohne den Bau von Prototypen bereits am Computerbildschirm durchführen. Dazu erfolgt auch eine Datenübergabe aus EPLAN Harness proD an das MCAD-System, sodass die Geometrie des Kabelbaums automatisch in allen Kollisionsprüfungen berücksichtigt wird. Die mechanische und elektrische Komponente des Prototypen gelangen – bereits in optimierter Form – zeitgleich auf den Prüfstand, wo sie miteinander ‚verheiratet‘ werden und sofort für Tests zur Verfügung stehen. Heinz Aitzetmüller über die erfreuliche Auswirkung: „Durch Parallelisierung der mechatronischen Produktentwicklung können wir unseren Kunden dabei helfen, die Produktentwicklungszeit beträchtlich zu verkürzen.“
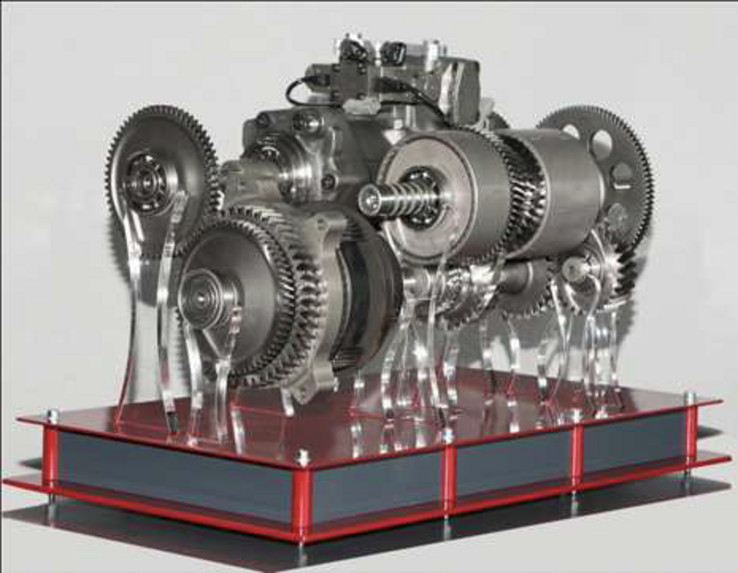
Die Verbesserung der Effizienz landwirtschaftlicher und kommunaler Nutzfahrzeuge ist Zweck der patentierten stufenlosen Automatikgetriebe VTP und VPD der VDS-Getriebe GmbH.
© VDS