Schaeffler: Rationelles Elektro-Engineering in „Losgröße Eins“
Die Schaeffler-Gruppe sieht sich im anspruchsvollen Bereich der Antriebstechnik als Innovationsführer und hat am zentralen Standort Schweinfurt eine eigene Abteilung für den Prüfstandsbau.
Er heißt Astraios, wiegt 350 Tonnen und kann Kräfte von insgesamt 10 Meganewton aufbringen – das entspricht einer Belastung von 1000 Tonnen. Die Rede ist von dem neuen Prüfstand, den Schaeffler kürzlich am Standort Schweinfurt in Betrieb genommen hat. Mit ihm werden die Großwälzlager geprüft, die vor allem in Windkraftanlagen zum Einsatz kommen. Das anspruchsvolle Projekt haben der hauseigene Prüfanlagenbau und Sondermaschinenbau in kurzer Planungs- und Bauzeiterfolgreich abgeschlossen. Die komplette Elektrotechnik des Prüfstandes wurde mit EPLAN Electric P8 geplant. Großwälzlager, die vor allem in Windkraftanlagen der Multi-Megawatt-Klasse zum Einsatz kommen, habenunter sehr dynamischen Belastungen eine Lebensdauer von mindestens zwanzig Jahren. Dabei stoßen die Entwickler oft an Grenzen der Werkstoff-, Tribo- und Konstruktionstechnik. Umso wichtiger sind umfassende Prüfstandsversuche. Die Schaeffler-Gruppe sieht sich in diesem anspruchsvollen Bereich der Antriebstechnik als Innovationsführer und hat am zentralen Standort Schweinfurt eine eigene Abteilung für den Prüfstandsbau. Die Elektroplaner in dieser Abteilung arbeiten seit rund 25 Jahren mit CAE-Software von EPLAN. Zwar handelt es sich bei einigen Projekten um Sonderanlagen, die in Losgröße 1 gefertigt werden. Aber die Elektrokonstrukteure haben in der Software EPLAN eine umfassende Bibliothek von Makros angelegt, die als Systembausteine bei neuen Projekten verwendet werden können und damit die Konstruktionszeit deutlich verkürzen. Die Makros bilden alle wiederkehrenden elektrischen Komponenten und Funktionen ab. Sie wurden bewusst klein granuliert, um auch bei ungewöhnlichen Anforderungen möglichst viele Bauteile aus der Bibliothek zu nutzen. So können die Elektro-Konstrukteure auch große Projekte rationell abarbeiten und sämtliche Schaltanlagen nach identischen Grundsätzen planen. Hohe Komplexität der Antriebs- und Messtechnik
Ein solches Großprojekt stand Ende 2009 bevor, als Schaeffler für den Standort Schweinfurt mit der Planung eines neuen Prüfstandes für Großwälzlager (Bild 1) begann. Die Ansprüche waren hoch: Es sollte der weltgrößte Prüfstand dieser Art sein, der Lager bis 3,50 Meter Außendurchmesser den typischerweise auftretenden Belastungen unterzieht. Derartige Großlager kommen künftig in Windkraftanlagen mit bis zu 6 MW Leistung zum Einsatz.
Für die Elektrokonstrukteure war die Herausforderung, dass die Steuerung auf der Antriebsseite sehr komplexe, überlagerte Bewegungen abbilden soll. Rund 450 digitale Eingänge und 260 Ausgänge wurden benötigt. Hinzu kamen die Schmieraggregate für den Prüfling mit 12 Dosiereinheiten, die sich exakt regeln lassen. Auf der messtechnischen Ebene waren rund 350 Sensoren und entsprechend viele analoge Eingänge und Auswertemöglichkeiten vorzusehen. Trotz großer Erfahrung im Prüfanlagenbau beschritt das rund 20 Mitarbeiter starke Team unter Projektleiter Reinhold Korn (s. Bild 2) somit in vielerlei Hinsicht Neuland. Dabei war die Planungs- und Bauzeit mit nur zwei Jahren veranschlagt – das ist vergleichsweise kurz für eine derart komplexe Sonderanlage, die immerhin rund 350 Tonnen wiegt und eine elektrische Anschlussleistung von 2200 A erfordert. Neue Plattform beschleunigt Konstruktion
Aus diesem Grund mussten Leonhard Keller und Heiko Gründl, verantwortlich für die Elektrokonstruktion, zeitgleich mit der mechanischen Konstruktion arbeiten. Und sie mussten eine weitere Herausforderung meistern: Der Großprüfstand war das erste Projekt, das sie mit EPLAN Electric P8 bearbeiteten. Da es sich hier im Vergleich zu EPLAN 5.70, dem Vorgängersystem, um eine ganz neue System-Plattform handelt, entsprach diese Vorgehensweise nicht ganz dem Lehrbuch: Normalerweise würde man ein kleineres Projekt für den Einstieg wählen und nicht das bislang Ambitionierteste überhaupt. Allerdings kam den Planern hier zugute, dass sie die vorhandenen Makros aus EPLAN 5.70 auf die neue EPLAN Plattform migrieren konnten. Und sie profitierten davon, dass EPLAN Electric P8, das CAE-System der neuen Plattform, zahlreiche Einzelprozesse im Planungsablauf beschleunigt und damit ein deutlich rationelleres Arbeiten ermöglicht. Ein anspruchsvolles Projekt
Leonhard Keller und Heiko Gründl planten eine Elektroanlage, die aus den einzelnen Funktionen Hydraulik-, Schmieröl-, Antriebsschrank und Messrack besteht und insgesamt 9 Schaltschrank-Meter (zuzüglich 1,6 Meter Reserve) umfasst. Dabei haben sie interessante technische Innovationen umgesetzt. So werden die drei Hydraulikpumpen mit je 160 kW Leistung, die die Zylinder bewegen, kaskadenartig und ohne Unterbrechung bedarfsgerecht zugeschaltet. Den Regler für diese energiesparende Fahrweise hat Schaeffler selbst programmiert. Für die Steuerung des gesamten messtechnischen Prozesses– beginnend bei der Ansteuerung der Antriebe über die Datenmessung und -aufzeichnung bis zur Visualisierung – ist SARA verantwortlich, das „Schaeffler Automation System for Research & Development Applications“. Es generiert die Sollwerte der Windlasten, regelt die Servozylinder und sammelt die Messdaten. Die Messungen am bewegten Prüfling stellen auch besondere Anforderungen an die Übertragung der Messwerte. Viele Daten werden kabellos übermittelt. Auch Seriengeräte kommen zum Einsatz
In den Prüfstand wurden auch zwei Seriengeräte von Schaeffler integriert: ein Messsystem für die Schwingungsüberwachung, das Auskunft über den Zustand des Wälzlagers gibt, und ein Partikelzählsystem, das die Verschmutzungen im Lagerschmieröl überwacht. Bei diesen beiden Systemen war die Elektroplanung einfach: Die Zeichnungssätze konnten, genau wie die Geräte selbst, komplett in das Projekt integriert werden. Die ersten Tests auf dem neuen Prüfstand (Bild 4) zeigten: Messergebnisse und Berechnungen stimmen überein. Inzwischen nutzt die Abteilung „Versuch“ den Prüfstand intensiv, um nach Optimierungspotenzialen für die Entwicklung neuer Wälzlagergenerationen zu suchen, die auch deren Berechnungsgrundlagen weiter verbessern. In naher Zukunft: Integration der Fluidtechnik
Für die nahe Zukunft planen die Verantwortlichen der Elektro-/ Systemtechnik im Prüfanlagenbau die Erweiterung der EPLAN Plattform um die beiden Module EPLAN Fluid (für die Fluidtechnik-Konstruktion) und EPLAN Pro Panel (für den Schaltanlagenbau). Damit geht die Verantwortung für die Planung der Fluidtechnik von der mechanischen Konstruktion auf die Elektrokonstruktion über. Für diese geänderte Form der Arbeitsteilung sprechen auch die Abläufe im Prüfanlagenbau: Die Elektroplaner müssen dann nicht manuell die Pläne nachzeichnen, die sie von den Kollegen erhalten, sondern können direkt auf der vorhandenen Plattform weiterarbeiten. Astraios: Ein Gigant der Mess- und Prüftechnik
Die Großwälzlager, die Schaeffler für Windkraftanlagen der Multi-Megawatt-Klasse fertigt, haben Außendurchmesser bis 3,50 Meter und sind bis zu 15 Tonnen schwer. Diese Lager werden extrem hohen Belastungen ausgesetzt. Die bis zu 100 Tonnen schwere Nabe mit den Rotorblättern bringt radiale Lasten in das Lager ein; die hoch dynamischen Windkräfte erzeugen im Lager vor allem Axialbelastungen und Momente. Bei der Konstruktion von Großlagern für Multi-Megawatt-Anlagen, die diesen hohen Belastungen über die geforderte Lebensdauer von 20 Jahren standhalten, waren die Entwickler bislang im Wesentlichen auf Berechnungen angewiesen. Schaeffler kann nun auf ganz reale Daten zurückgreifen. Denn der neue Großprüfstand „Astraios“, der nach dem Vater der vier Windgötter in der griechischen Mythologie benannt ist, simuliert realitätsgetreu die Praxisbedingungen, denen die Wälzlager ausgesetzt sind. Dafür sorgen vier hydraulische Radialzylinder und vier Axialzylinder, die einzeln jeweils Kräfte von 1 bzw. 1,5 Meganewton (entsprechend 100 bzw. 150 Tonnen) erzeugen. Die Bewegungen können überlagert und hochdynamisch variiert werden – ganz so wie der Wind hoch oben an den Rotoren weht. Während der Lagerbewegung erfassen rund 350 Sensoren Werte wie Temperatur, Druck, Drehmoment und Dehnung, die visualisiert, dokumentiert und ausgewertet werden. Rund 7 Mio. Euro hat Schaeffler in diese Anlage investiert, die Wälzlager für Windkraftanlagen bis 6 MW Leistung prüfen kann. Damit ist Astraios nicht nur der modernste, sondern auch der größte und leistungsfähigste Großlagerprüfstand der Welt.
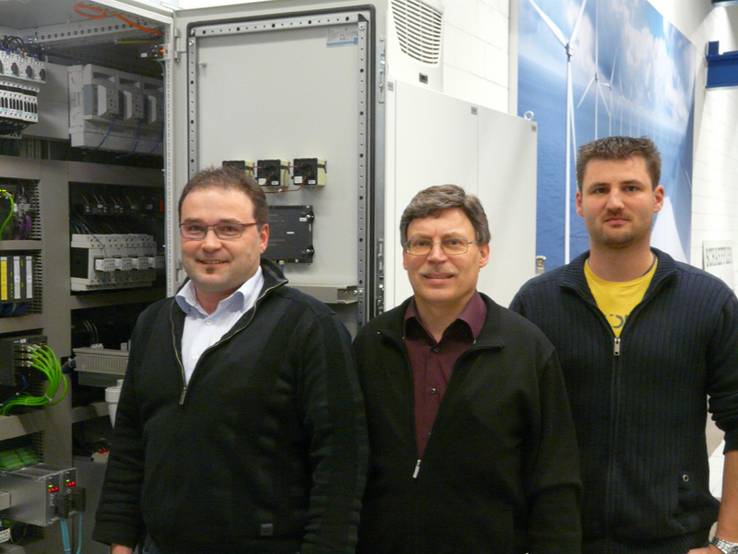
Die Elektroplaner des Schaeffler-Prüfanlagenbaus Leonhard Keller (links) und Heiko Gründl (rechts) mit Projektleiter Reinhold Korn (Mitte) vor einem der Schaltschränke des Prüfstandes.
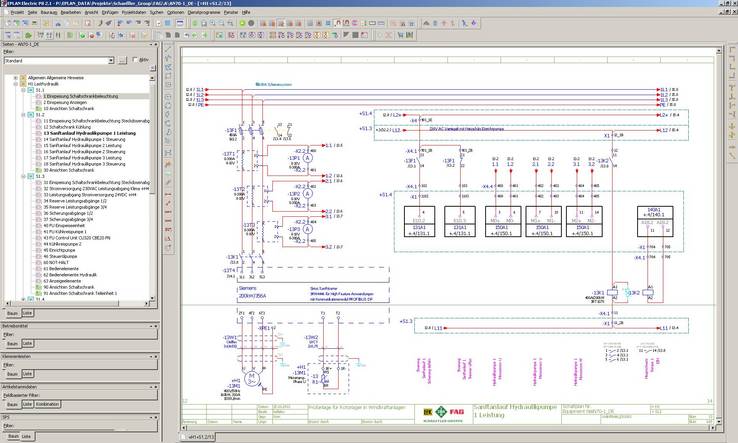
Vom Aufstellplan bis zum Detail: Die komplette Elektroplanung des „Astraios“-Prüfstandes wurde mit EPLAN Electric P8 erledigt.